Calcined Bauxite - Product
Calcined Bauxite
Calcined Bauxite is a high-quality, heat-treated form of bauxite ore, produced by the calcination process where bauxite is heated to high temperatures (approximately 800-1600°C) in rotary kilns or furnaces. This process removes moisture and converts the material into a more stable form, enhancing its hardness, thermal resistance, and chemical stability. Calcined Bauxite is widely used in the production of refractory materials, abrasives, and other industrial applications due to its high alumina content and robust physical properties.
- Product Category: Abrasive & Material
- Key Features:
- High Alumina Content: Contains a high percentage of aluminum oxide (Al₂O₃), typically 85-90%, providing a superior material for high-temperature and abrasive applications.
- Thermal Stability: Capable of withstanding high temperatures without significant degradation, making it suitable for use in refractory applications and environments subject to thermal stress.
- Chemical Resistance: Highly resistant to acids and alkalis, ensuring durability and stability in aggressive chemical environments.
- Hardness: Offers significant hardness, making it suitable for abrasive applications and as a raw material in the production of abrasives and refractories.
- Versatility: Can be processed into various forms, including granules, powders, and sintered products, to meet specific industrial requirements.
Applications:
Refractories: Used in the manufacture of refractory bricks, castables, and other high-temperature materials for furnaces, kilns, and reactors.
Abrasives: Employed in the production of abrasive materials such as grinding wheels, cutting tools, and blasting media due to its hardness and durability.
Ceramics: Applied in the production of advanced ceramic materials and components due to its high alumina content and thermal stability.
Steel Industry: Used as a flux in steelmaking and in the production of sintered alumina for high-performance steelmaking applications.
Industrial Flooring: Used in the production of industrial flooring and surfaces that require high resistance to wear and thermal shock.
Technical Specifications:
Chemical Composition:
Al₂O₃ (Aluminum Oxide): 85-90%
Fe₂O₃ (Iron Oxide): 3-5%
SiO₂ (Silicon Dioxide): 2-4%
Hardness: Mohs hardness of approximately 8-9
Density: Approximately 3.8-4.0 g/cm³
Melting Point: ~1550-1600°C
Particle Size: Available in various sizes from fine powders to coarse granules, customized based on application needs
Shape: Typically available as granular or powder form
Advantages:
High Alumina Content: Ensures high performance in applications requiring superior thermal and chemical resistance.
Durability: Offers excellent resistance to wear and thermal shock, enhancing the longevity and effectiveness of refractory and abrasive products.
Thermal and Chemical Stability: Performs well under extreme temperatures and in aggressive chemical environments, making it suitable for demanding industrial uses.
Versatile Applications: Adaptable for a wide range of uses, including refractories, abrasives, and ceramics.
Packaging: Available in 25 kg bags, 500 kg bulk bags, or as per customer specifications.
Storage:
Store in a dry, cool place. Ensure containers are tightly sealed to prevent contamination and moisture absorption.
You May Also Like
Provide more details here.
Use text and images to tell your company’s story. Explain what makes your product or service extraordinary.
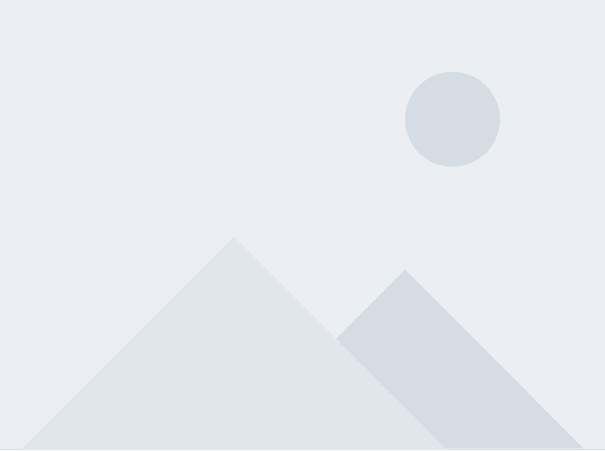
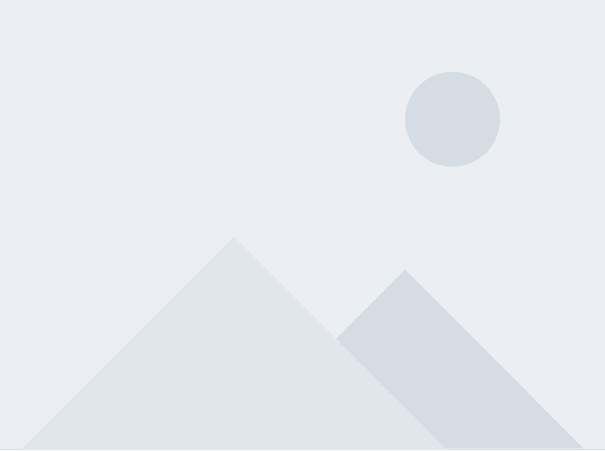
Provide more details here.
Use text and images to tell your company’s story. Explain what makes your product or service extraordinary.